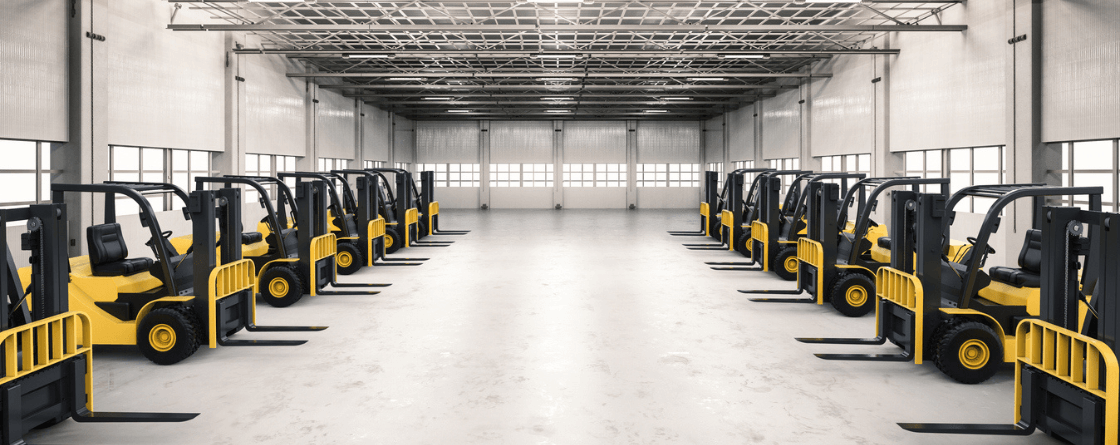
Blog
Essential Maintenance Tips for Telescopic Forklifts
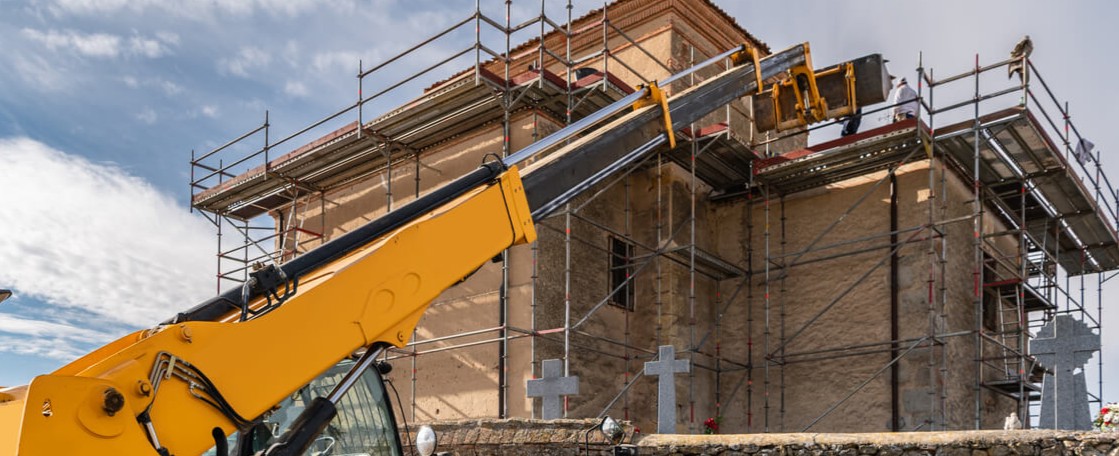
Telescopic forklifts, often referred to as telehandlers, are invaluable in demanding work environments like construction, logistics, and agriculture. Known for their reach and lifting capacity, machines like the Manitou telescopic forklift deliver performance and versatility on-site. However, to maintain this performance and protect your investment, regular and thorough maintenance is essential.
With decades of experience supporting industries that rely on heavy lifting equipment, Glosrose understands the challenges businesses face when keeping telehandlers in reliable working condition. Maintenance isn’t just a technical requirement, it’s a key part of staying productive, meeting health and safety standards, and avoiding unnecessary costs. This guide outlines practical maintenance steps to help you get the best out of your machine every day.
Why Maintenance Matters for Telescopic Forklifts
A telescopic forklift’s moving parts and hydraulic systems face considerable stress during daily use. Regular inspections and servicing are vital to prevent avoidable failures, reduce long-term repair costs, and ensure safe operation.
If you’re using a Manitou telescopic forklift, it’s especially important to follow manufacturer-recommended maintenance schedules. These machines often operate in rough conditions and carry heavy loads, so a proactive approach to servicing can significantly extend their working life.
Maintenance also supports legal compliance. Under the Provision and Use of Work Equipment Regulations (PUWER), all equipment must be maintained in a safe condition. Keeping service records and conducting regular checks helps businesses meet their obligations and reduce liability.
Daily Checks Before Operation
Start with a daily inspection before using your telescopic forklift. This routine ensures the equipment is safe and fully operational.
- Visual inspection: Check tyres for wear or damage, look for fluid leaks, and inspect the boom for cracks or distortion.
- Hydraulic fluid: Ensure fluid levels are within range and there are no signs of contamination.
- Tyre pressure and condition: Under-inflated tyres can affect stability and handling, while worn tyres may compromise safety.
- Lights and indicators: Confirm all safety lights, brake lights, and indicators are working.
- Forks and attachments: Make sure forks are not bent or cracked, and that attachments are secure and functioning correctly.
Documenting these checks allows you to track wear trends and spot recurring issues early.
A well-organised checklist also creates consistency across operators. Having a shared reference ensures that small but critical details aren’t missed and that every team member contributes to equipment safety.
Weekly and Monthly Maintenance Tasks
Beyond daily inspections, schedule weekly and monthly tasks to catch potential problems that may not be immediately visible.
- Lubricate pivot points and joints to prevent wear and reduce friction.
- Clean filters and check air intake systems to prevent debris from affecting performance.
- Inspect the mast and boom extension for alignment, cracks, or signs of unusual stress.
- Review brake and steering systems for responsiveness and fluid condition.
- Check warning labels and decals to ensure all safety information is visible and legible.
It’s also a good idea to review operator feedback weekly. Minor complaints—such as increased vibration, slower lifting speeds, or reduced engine response—often signal early-stage mechanical issues that may not show up in a visual inspection.
Preventative checks like these improve reliability and reduce unexpected breakdowns.
Quarterly and Annual Servicing
These more in-depth maintenance checks should be carried out by qualified technicians, especially for Manitou telescopic forklifts where complex hydraulics and electrics are involved.
- Hydraulic system inspection: Check for hose wear, fluid degradation, and proper pressure levels.
- Engine servicing: Replace filters, check belts, inspect coolant systems, and assess engine performance.
- Transmission and axle checks: Look for leaks, assess gear changes, and confirm lubricant levels.
- Chassis and boom wear: Inspect for cracks, corrosion, and misalignment, particularly where structural stress is high.
Servicing intervals may vary based on usage intensity, operating environment, and model type. For example, forklifts used in dusty construction sites may require more frequent filter replacements and cooling system checks than those operating in enclosed warehouses.
At Glosrose, our servicing teams carry out these procedures according to manufacturer standards, using OEM parts to maintain reliability and warranty compliance.
Signs Your Telescopic Forklift Needs Immediate Attention
Even with routine maintenance, unexpected faults can occur. Operators should know what to look out for:
- Hydraulic lag or jerky movements when extending the boom.
- Unusual engine noise, especially under load.
- Warning lights that persist despite resets.
- Oil patches under parked machines, indicating potential leaks.
- Reduced lifting capacity or visible tilt during lifting.
Any of these symptoms should trigger an immediate inspection. Continuing to operate a faulty Manitou telescopic forklift can lead to serious safety risks and expensive mechanical failures.
Operator Training and Handling Practices
Proper operation plays a big role in reducing wear and extending equipment life.
- Avoid overloading – always stay within the stated capacity for the specific boom extension.
- Operate smoothly – sharp turns, sudden stops, and erratic lifting can strain hydraulics and structure.
- Store on level ground – reduces stress on axles and stabilisers.
- Secure the boom and forks when not in use.
Regular refresher training ensures that both new and experienced operators understand how to reduce strain on the equipment. It also reinforces safety practices and helps standardise procedures across teams.
Glosrose also offers operator training to help your team understand best practices and safety protocols.
Using Glosrose for Maintenance and Support
When you work with Glosrose, you get more than access to forklift sales, you get a reliable partner with decades of experience in maintenance and aftercare.
- Flexible servicing plans – tailored to your usage, fleet size, and site requirements.
- OEM-approved parts – protecting machine integrity and resale value.
- On-site and workshop servicing – convenient options to minimise downtime.
- Expert support for Manitou models – including diagnostics, repair, and fleet health reporting.
We also offer maintenance record management, giving you full visibility over your servicing history and helping with audit readiness.
If you’re considering a new or used Manitou telescopic forklift, our team can also help match you with the right model for your lifting tasks and terrain requirements.
Keep Your Operations Moving with Glosrose
A well-maintained telescopic forklift ensures safer operations, improved efficiency, and better long-term return on investment. Maintenance is not just about preventing breakdowns, it’s about protecting your team, your schedule, and your bottom line.
Glosrose offers the expertise, servicing, and product support to keep your equipment performing when it matters most. Our team helps you stay ahead of issues, reduce downtime, and get the best value from your fleet.
Ready to improve your uptime and extend the lifespan of your Manitou telescopic forklift? Contact Glosrose for expert maintenance plans, dependable aftercare, and tailored advice to meet your operational needs.
Call us on 01622 880669 or visit glosrose.co.uk to get started.
You May Also Like
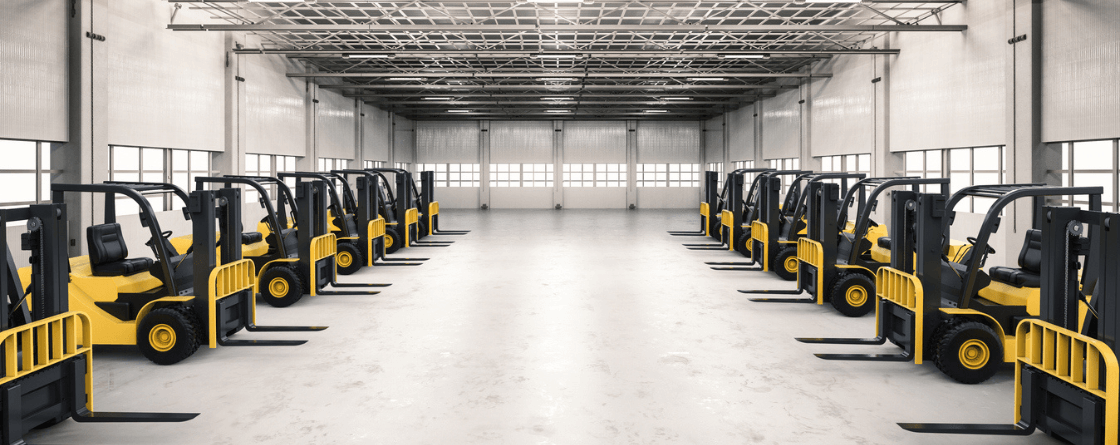
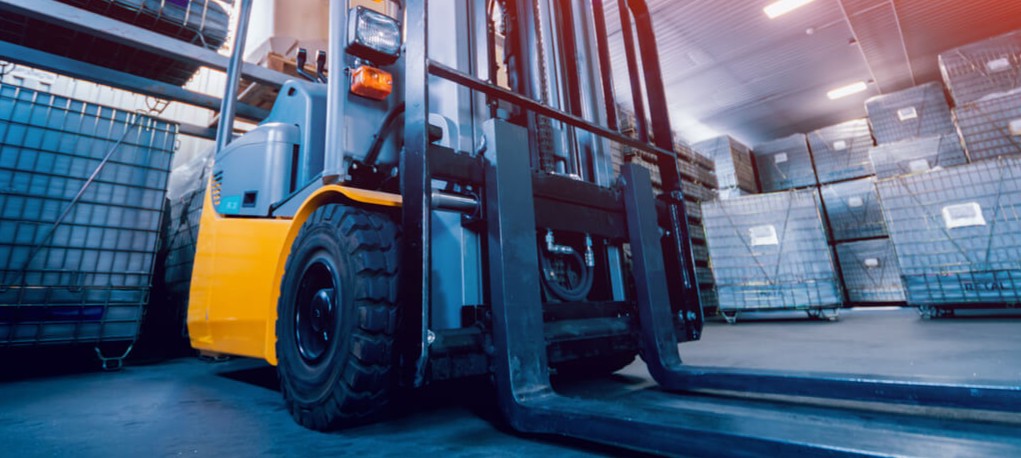
How to Match the Right Forklift to Your Warehouse Layout
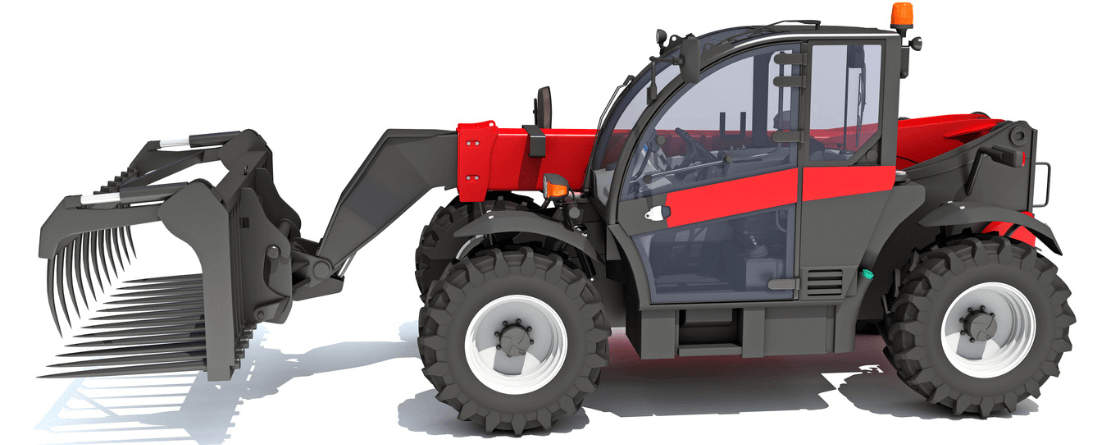
How to Choose the Right Manitou Telehandler for Confined or Uneven Terrain
Get in Touch
Not sure what you are looking for or need some advice for your requirements? Get in touch with us today and a member of our experienced team will be more than happy to help answer your questions.