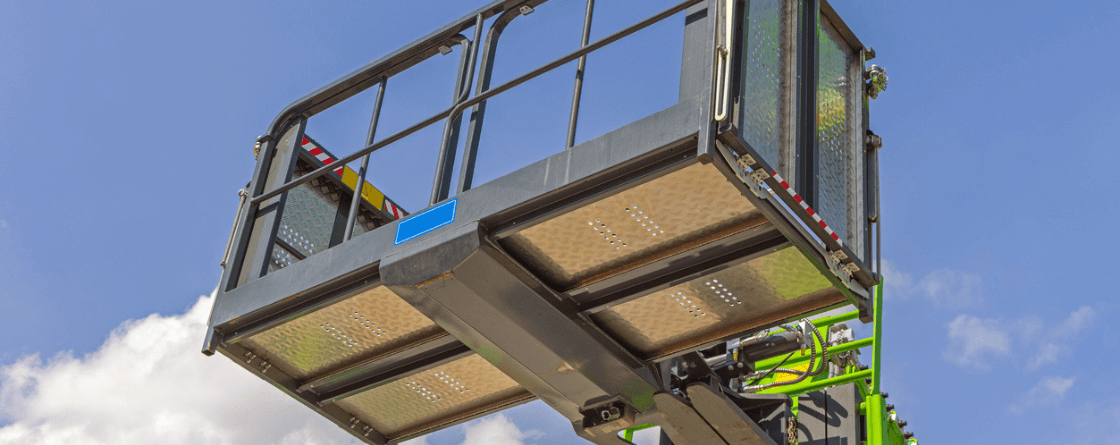
Blog
Hiring Forklifts for Seasonal Staff? Avoid These Operator Handover Mistakes
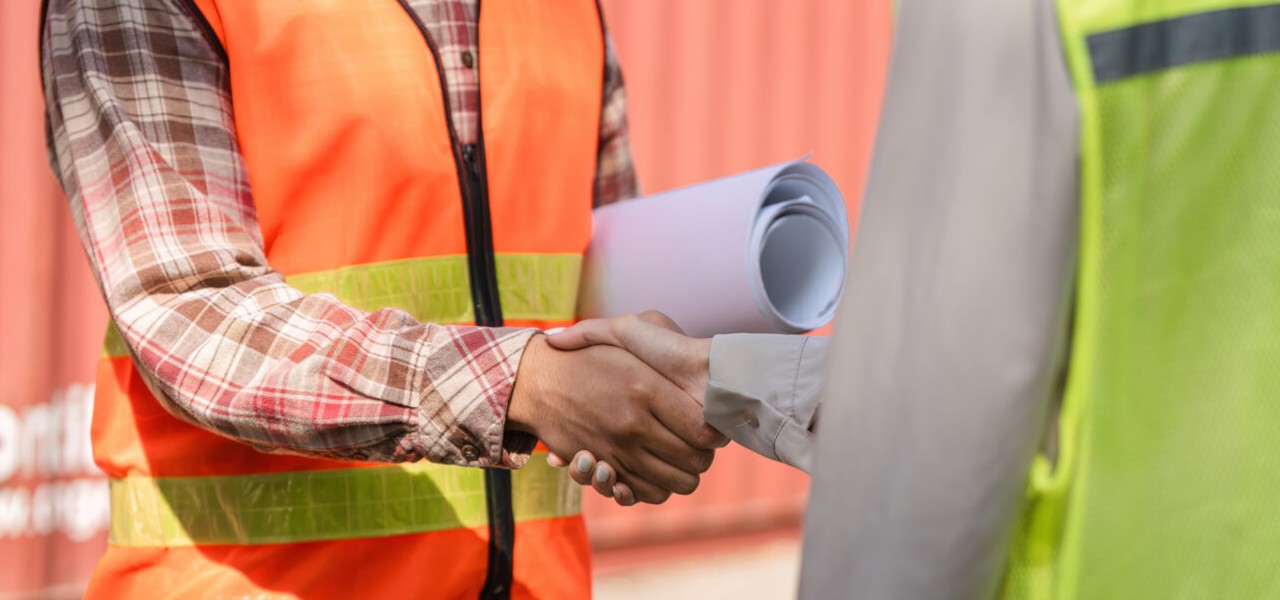
One missed step during handover can cost you thousands in damage or downtime.
Seasonal hires arrive fast. They’re needed on the floor yesterday. But if your forklift hire shows up and no one gives the operator a clear briefing, you’re gambling with your operation.
We’ve seen the result: bent racking, dropped pallets, and preventable injuries all which stem from skipping a structured handover. Here’s how to avoid the most common and costly mistakes and ensure every seasonal forklift hire runs smoothly.
Why are handovers skipped and why does it matter?
Busy managers often assume that an experienced operator can simply hop on and get going. But assuming every driver knows your forklift model or understands your site layout is risky. No two warehouses are the same.
Even seasoned drivers need:
- Time to understand site-specific traffic rules
- Familiarity with different makes or models of forklifts
- Awareness of loading dock layouts and blind spots
For operators who haven’t driven in a few months, this context is even more critical.
In warehouses with multilingual teams, language differences can further complicate communication. Visual guides, universal symbols, and clear demonstrations can save time and reduce risk.
Every effective handover builds trust. Seasonal staff who receive proper onboarding perform with more confidence and make fewer errors.
What makes a forklift handover effective?
A good handover should be concise, visual, and hands-on. Operators absorb more when they’re shown rather than told.
Here’s what to include:
- Control walkthroughs: Explain unique features or controls
- Weight limits and load handling: Tailored to daily tasks
- Site-specific risks: Flag docks, narrow passages, and slopes
- Emergency steps: Show location of fire exits, alarms, and procedures
Assign a trained team member to shadow new operators during their first shift. They can answer quick questions and reinforce key points.
Follow-up matters too. A five-minute check-in the next day helps reinforce safety and clarify anything missed.
What questions should you ask your forklift hire company?
Before you finalise a forklift hire, take a few moments to ask the right questions:
- When was the forklift last serviced?
- What safety features are included?
- Do you provide model-specific handover materials?
Your hire partner should be able to answer clearly and help you prepare for the season ahead. If they can’t, look elsewhere.
How can you prepare before the forklift even arrives?
Preparation helps your team hit the ground running. It also cuts down the time your equipment sits idle.
Tips that make a big difference:
- Send out pre-start guides or operator videos
- Share safety signage and floor markings in advance
- Assign one experienced operator as a buddy system
- Keep laminated cheat sheets inside every cab
You can also run a five-minute safety briefing before the first shift starts. Remind teams of daily checks, PPE policies, and pedestrian awareness.
And make sure your forklift hire supplier delivers machines ready to use with fluids topped up, tyres checked, and paperwork included.
How do you minimise downtime during seasonal peaks?
Seasonal periods come with tighter deadlines and more pressure. One poorly briefed operator can cause delays that impact the whole warehouse.
- Make sure each new operator knows the site layout.
- Include pallet handling instructions during handover.
- Provide a single point of contact for issue resolution.
Minimising downtime starts with making sure every operator is ready from day one.
Do seasonal forklift drivers need training?
Yes. The law requires all operators to be properly trained, regardless of contract length.
Here’s what to check:
- Valid certificates from an accredited training body
- Refresher training if they haven’t driven in 12+ months
- Site-specific induction tailored to your workplace
A forklift hire provider should help guide you on the right training level. Glosrose works closely with clients to ensure temporary staff meet the same safety expectations as permanent team members.
Ignoring training isn’t just risky but legally negligent with some serious repercussions. If something goes wrong, insurance may not cover you.
Can a bad handover affect your hire agreement?
Yes, and the consequences aren’t small.
Most forklift hire contracts outline user responsibilities, which include damage prevention, proper operation, and adherence to site safety standards. If an untrained operator causes damage, you’re liable.
What poor handovers often lead to:
- Misuse of lifting capacity
- Failure to complete daily checks
- Driving without regard for floor conditions or gradients
All of these can shorten the life of your hired machine or create dangerous working conditions.
Forklift damage can also delay operations. Replacing or repairing machines mid-season disrupts schedules and frustrates customers.
Will my forklift hire company help with onboarding?
A good hire company won’t just drop the forklift off and leave. At Glosrose, we provide:
- Setup support and safe-use guidance
- Recommendations based on operator skill levels
- Optional extras like safety lights, cameras, and ergonomic seats
We’re proactive in helping our clients prepare their teams for safe and productive use. That includes offering handover materials tailored to the forklift model and use case.
Hiring seasonal staff doesn’t mean lowering safety standards. The right support ensures everyone’s ready.
What are the most common forklift handover mistakes?
The same avoidable issues come up time and again:
- Skipping licence checks or inductions
- Not pointing out model-specific controls
- Failing to brief on hazards or daily routines
- Using a generic approach instead of site-specific guidance
To counter these:
- Use a checklist every time
- Encourage open communication from operators
- Update floor signage if your layout changes
Even five minutes of focused attention on these points can save hours of downtime.
Are handovers worth the time?
Some managers view handovers as a tick-box task. But when something goes wrong, the first question is always: was the operator properly inducted?
A forklift accident can lead to:
- Worker injury
- Stock loss
- Legal action
Taking the time to brief seasonal operators sets the tone. It signals that safety matters and that every team member is accountable.
Get seasonal forklift hire right from the start
Hiring forklifts to support seasonal demand can be smart and cost-effective. But only if operators are properly onboarded.
Glosrose provides forklift hire across a wide range of industries, with expert guidance and ongoing support. We help you avoid costly mistakes by making sure your staff get the tools and training they need.
Talk to Glosrose to book seasonal forklift hire with confidence and peace of mind.
You May Also Like
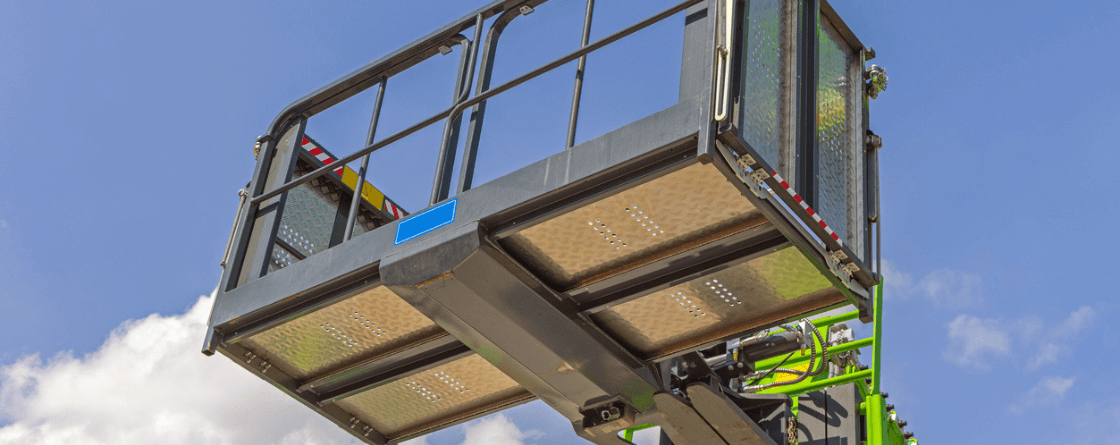
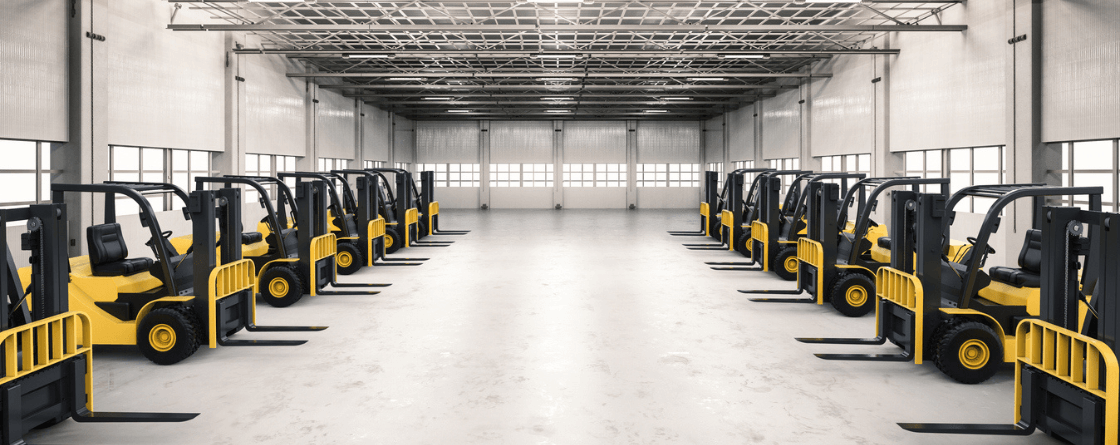
Seasonal Forklift Demand: How to Prepare Your Fleet for Peak Periods
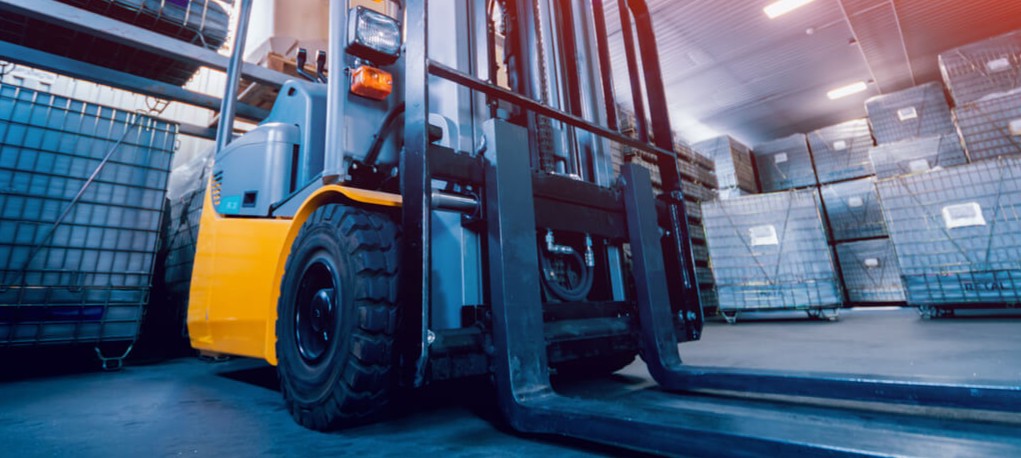
How to Match the Right Forklift to Your Warehouse Layout
Get in Touch
Not sure what you are looking for or need some advice for your requirements? Get in touch with us today and a member of our experienced team will be more than happy to help answer your questions.