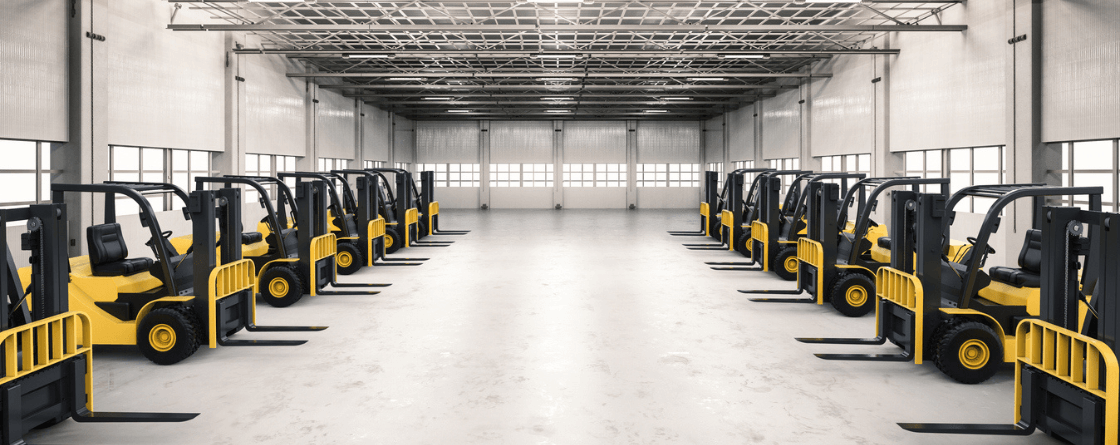
Blog
Forklift Maintenance: What to Expect When You Hire
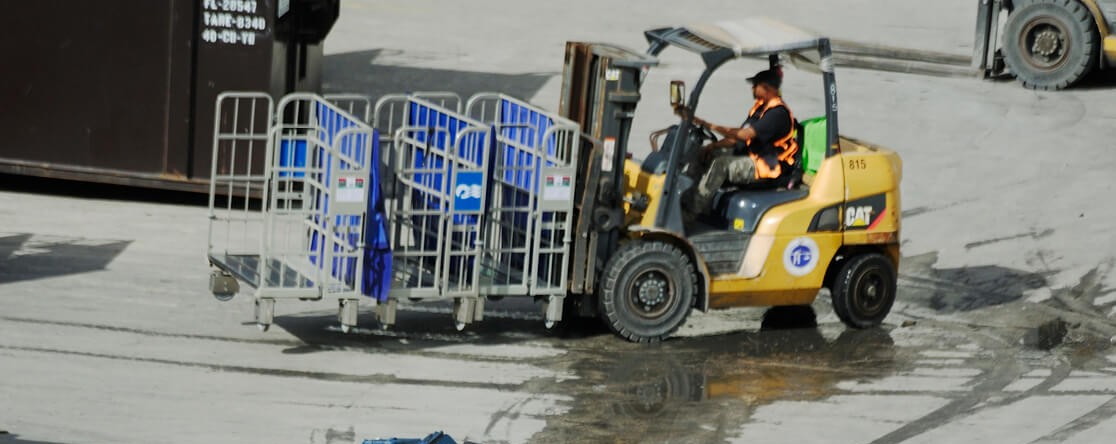
Why Forklift Maintenance Matters When Hiring
Unexpected forklift breakdowns can bring operations to a standstill. Whether in a warehouse, construction site, or logistics hub, businesses rely on forklifts to move heavy loads efficiently. But what happens when a hired forklift suddenly stops working? Delays, lost productivity, and unexpected repair costs quickly add up.
Forklift maintenance plays a fundamental role in preventing these issues, yet many businesses overlook it when hiring equipment. Without proper servicing, a forklift can become a liability rather than an asset. The key to a successful forklift hire is choosing a provider that prioritises maintenance and delivers reliable, well-serviced machines that can perform without disruption.
At Glosrose, we take maintenance seriously. Our comprehensive forklift hire solutions ensure that every machine is in peak condition before delivery and remains that way throughout the hire period. With proactive servicing, emergency support, and expert inspections, we help businesses avoid costly downtime and keep their operations running smoothly.
Common Challenges with Forklift Hire and How Maintenance Solves Them
Hiring a forklift offers flexibility and cost savings, but improper maintenance can create operational risks. Common challenges businesses face include:
- Unplanned downtime – A poorly maintained forklift can fail mid-operation, causing delays.
- Unexpected repair costs – If servicing is not included in the hire agreement, businesses may end up paying for breakdowns.
- Safety concerns – Worn-out tyres, faulty brakes, or hydraulic issues can pose risks to operators.
- Inconsistent performance – A forklift that isn’t serviced regularly may lose power, stability, or lifting efficiency.
- Regulatory non-compliance – Failing to maintain forklifts properly can result in fines or legal issues, particularly in industries where safety compliance is heavily regulated.
- Short-term vs. long-term hiring concerns – Businesses may not always know how to balance short-term efficiency with long-term operational needs when hiring forklifts.
A professional forklift hire service should eliminate these issues with routine maintenance, thorough inspections, and expert servicing. Glosrose ensures every hired forklift meets strict performance and safety standards, giving businesses peace of mind.
What to Expect from a Well-Maintained Hired Forklift
1. Pre-Hire Inspection and Servicing
Before delivery, a hired forklift should undergo a comprehensive inspection to ensure reliability. At Glosrose, our technicians check:
- Tyres and wheels – Ensuring tread depth is sufficient for grip and stability.
- Braking system – Testing foot brakes, handbrakes, and emergency stop functions.
- Hydraulics and lifting mechanisms – Confirming smooth lifting, lowering, and tilting.
- Battery and fuel systems – Ensuring electric models are fully charged and internal combustion engines run efficiently.
- Mast and forks – Inspecting for wear, cracks, or bending that could impact performance.
- Operator controls and safety features – Ensuring all levers, warning systems, and seat belts function correctly.
By conducting these checks, Glosrose guarantees that each forklift hire meets industry standards, reducing the likelihood of performance issues.
2. Routine Maintenance During the Hire Period
Regular maintenance keeps hired forklifts operating efficiently. A reputable hire provider should include scheduled servicing to prevent breakdowns. Glosrose forklift hire agreements include:
- Lubrication of moving parts – Reducing wear and prolonging the forklift’s lifespan.
- Hydraulic fluid checks – Preventing leaks and ensuring smooth operation.
- Brake and steering system inspections – Maintaining safety and control.
- Battery and charging system maintenance – Extending the life of electric forklifts.
- Tyre inspections and replacements – Preventing accidents caused by worn-out tyres.
- Software updates and diagnostic checks – Keeping forklifts up-to-date with the latest performance and safety enhancements.
These routine services minimise downtime and ensure forklifts remain in peak condition for the duration of the hire.
3. Emergency Repairs and Support
Even with regular servicing, occasional faults can occur. Reliable forklift hire services include fast-response support to handle emergency repairs.
At Glosrose, our maintenance team provides rapid on-site repair services, ensuring minimal disruption to your operations. We supply:
- Replacement parts and spare forklifts – If a forklift cannot be fixed on-site.
- 24/7 breakdown assistance – For urgent repairs.
- Technical support – To troubleshoot minor issues and avoid unnecessary delays.
- Remote diagnostics and troubleshooting – Quickly identifying issues before they lead to equipment failure.
With Glosrose’s forklift hire service, businesses can focus on operations without worrying about unexpected maintenance challenges.
How Glosrose Ensures Reliable Forklift Hire
When hiring a forklift, partnering with a trusted provider is essential. Glosrose guarantees well-maintained forklifts, backed by expert servicing and ongoing support.
Our Commitment to Quality Forklift Hire:
- Comprehensive servicing before and during the hire period.
- Fast-response maintenance to minimise downtime.
- Flexible hire contracts that include servicing and repair costs.
- A wide range of forklifts, from electric to diesel models, to match different operational needs.
- Industry expertise and compliance support – Helping businesses meet safety and regulatory standards.
- Proactive maintenance schedules – Ensuring that forklifts operate at peak performance at all times.
By choosing Glosrose for forklift hire, businesses reduce operational risks, improve productivity, and ensure reliable performance from start to finish.
Additional Tips for Getting the Most Out of Your Hired Forklift
To ensure you maximise the benefits of your forklift hire, consider the following best practices:
- Train your operators – Proper training helps prevent wear and tear caused by improper use.
- Stick to load capacity limits – Overloading can strain the forklift and lead to breakdowns.
- Conduct daily inspections – Operators should check for leaks, unusual noises, and tyre wear before using the forklift each day.
- Report minor issues early – Small faults can escalate into costly repairs if left unchecked.
- Choose the right forklift for the job – Ensure the hired forklift has the right capacity, power type, and attachments for your specific needs.
Glosrose provides expert consultation to help businesses make informed hiring decisions and implement best practices for forklift use.
Get Reliable Forklift Hire with Glosrose
Forklift hire should be hassle-free, with maintenance included to ensure smooth and safe operation. At Glosrose, we provide fully serviced forklifts with flexible hire terms, expert maintenance, and rapid repair support.
Our team ensures that every forklift hire is ready for immediate use, fully inspected, and backed by comprehensive servicing throughout the rental period.
Don’t let forklift maintenance disrupt your operations. Contact Glosrose today at 01622 880669 or visit glosrose.co.uk to find the perfect forklift hire solution for your business.
You May Also Like
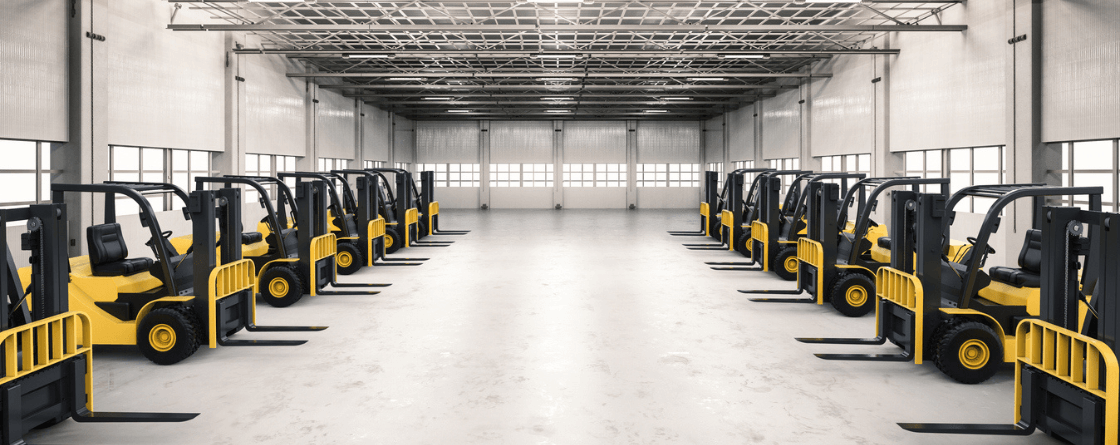
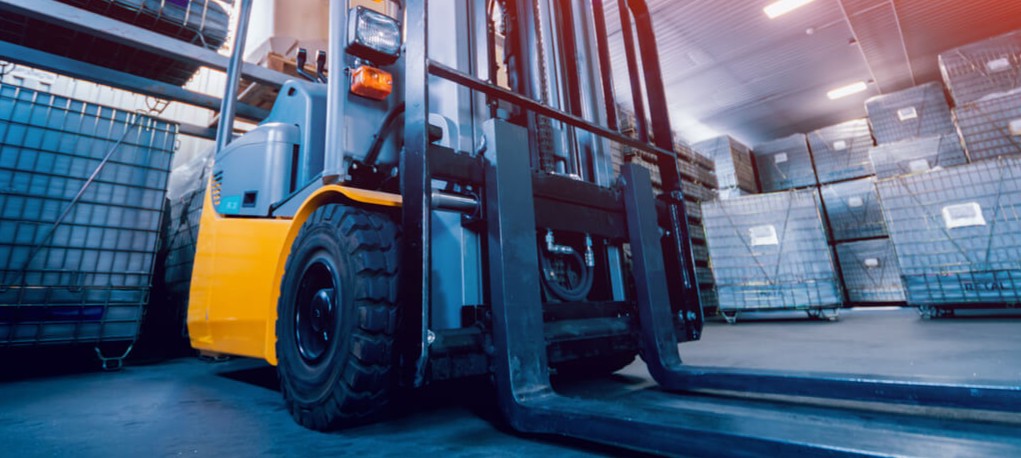
How to Match the Right Forklift to Your Warehouse Layout
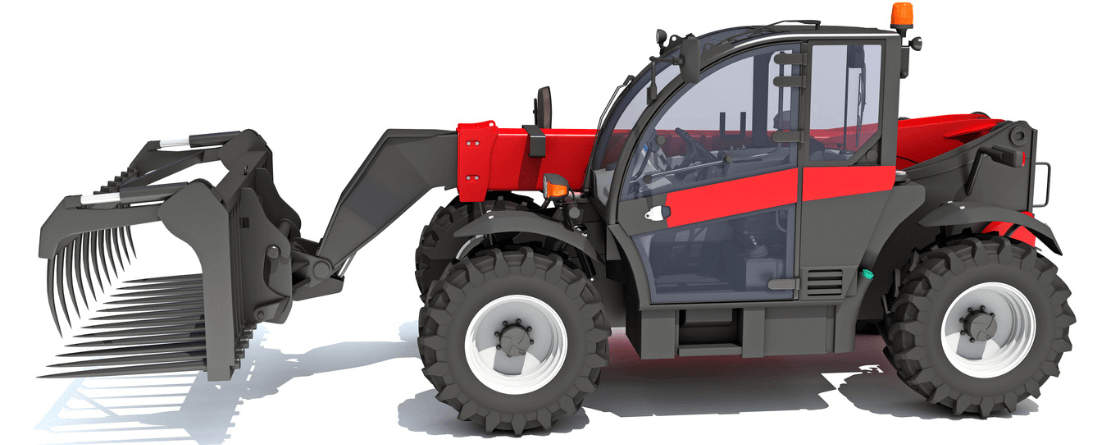
How to Choose the Right Manitou Telehandler for Confined or Uneven Terrain
Get in Touch
Not sure what you are looking for or need some advice for your requirements? Get in touch with us today and a member of our experienced team will be more than happy to help answer your questions.